Struggles Persist for American Manufacturers as they Strive to Relocate Supply Chains Within U.S., According to Wall Street Journal
Struggling to go all-American? That's the new challenge facing U.S. manufacturers, according to a report by The Wall Street Journal. They're finding it tough to source every single component domestically, with essential materials either hard to come by, expensive as all get-out or produced in meager quantities stateside.
Take Decked, an Idaho-based company, for instance. They're running into roadblocks when it comes to sourcing critical materials like certain types of steel, electronics and plastics. Even when U.S. supplies are available, a lot of these materials come up short when it comes to quality or production capacity.
The situation isn't helped by the fact that federal regulations are stacked against 'em. The FTC's "Made in USA" rules demand near-total domestic sourcing, meaning manufacturers either need to overhaul their supply chains or forego the marketing advantage. Plus, verifying country-of-origin adds a whopping 5-7 days to processing times.
Then there's the cost and lead-time pressures. With domestic component shortages, raw material costs can skyrocket by 15-40% and lead times for critical parts can stretch out by 6-12 weeks. Building up a domestic parts stockpile only increases working capital needs by up to 35%.
Inflexibility is another snag. Smaller manufacturing companies have a harder time adjusting to urgent orders or design changes when they're locked into limited domestic supplier networks. Production adjustments often require drawn-out requalification processes.
Transitions towards domestic sourcing don't come cheap, either. Building up domestic suppliers for critical components requires substantial infrastructure investment, with up to 20% of technology budgets diverted to supply chain restructuring. Plus, redesigning products to accommodate local materials can place a heavy strain on resources.
While the pandemic has sparked a reshoring trend among manufacturers, these structural barriers make swift transitions tricky, especially for small-scale companies. They often don't have enough resources to absorb the compliance and procurement overhauls that come with the territory.
- "Despite struggling to source components domestically, Decked, a company based in Idaho, continues to face roadblocks in acquiring critical materials like certain types of steel, electronics, and plastics essential for their production."
- "The finance industry can attest to the escalating costs of raw materials due to domestic shortages, as these can skyrocket by 15-40%, according to the business reports."
- "Manufacturers, including those like Deckd, are grappling with lead-time pressures, as critical parts can stretch out by 6-12 weeks due to domestic component shortages."
- "Amidst the challenges of shifting to domestic sourcing, transition costs for small-scale companies can be burdensome, as it may require up to 20% of their technology budgets for supply chain restructuring."
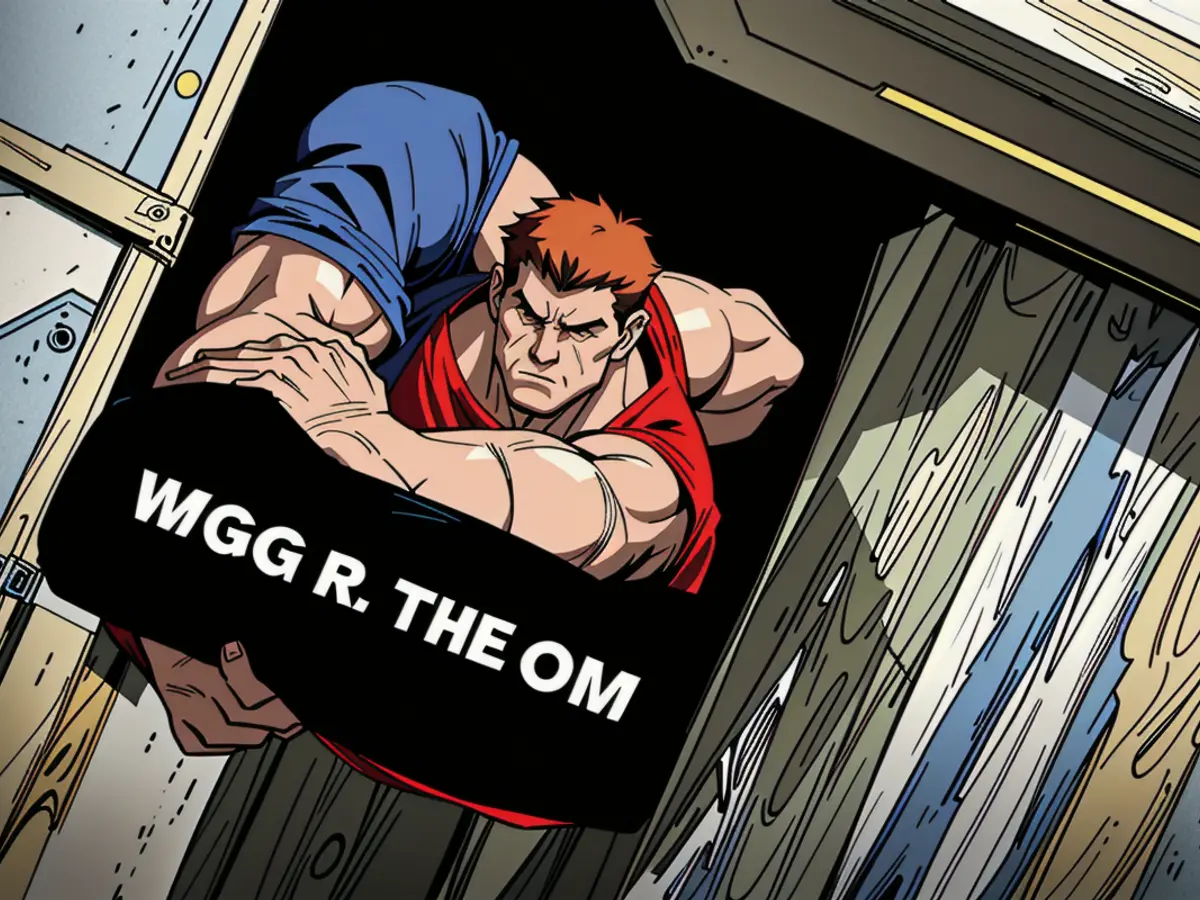